innovative solutions from engineering to manufacturing
Sonaca is highly skilled in designing, certifying, testing, producing, and assembling movable components for aircraft wings, like slats, flaps, ailerons, and spoilers. This also covers the mechanisms for wing ice protection systems and fairings. We create cutting-edge solutions using both metal and composite materials to deliver top-notch, effective, and trustworthy integrated structures. Sonaca can tailor our solutions to fit any type of aircraft and production rate.
Leading Edge Slats
Sonaca offers a very wide panel of slats tailored to meet the specific requirements of all customers. Our offerings include integrated metallic and composite solutions for leading edges, as well as slat track mechanisms and ice protection systems using both pneumatic and electric technology. We offer complete plug-and-fly solutions with final finishing and polishing services.
Flaps
Sonaca successfully extents its broad expertise in control surfaces with reliable industrial & responsive solutions for the flaps, flaps fairing and mechanisms. Thanks to the latest technologies developed by Sonaca such as out-of-autoclave processes RTM, SQRTM and automatic processes ATL, Sonaca offers best global price and reduction of aircraft fuel burn.
Ailerons & spoilers
In the focus of reducing weight and costs, Sonaca is developing SQRTM processes for composite ailerons. Their design led to an improvement in parts quality, meaning tighter tolerances and better aerodynamic smoothness with a lure towards fuel consumption reduction. Our engineers put a great effort to optimize the reparability and the maintenance of ailerons.
Reliable trailing-edge movables has become a major consideration for Sonaca. Parts quality improvement and part count reduction is something our engineers deal with every day. Our one-shot composite spoilers, combining SQRTM and ATL processes, allow closer time to market as well as environment durability and robustness.
Complex & Nose Fuselages
Sonaca combines its engineering, certification, manufacturing and assembly capabilities to offer the most adapted solutions in forward, center and rear fuselage sections. The group’s expertise in virtual testing offers the unique advantage of providing optimized geometries solutions to these high-loaded interfaces concerns.
Sonaca has expertise in the manufacturing of big and small elementary parts, from control surfaces to fuselage parts. Our long-term experience in aircraft structures provides a solution to these complex and highly loaded interfaces. Our well established automated production lines allow us to reach world’s largest aircrafts dimensions.
Engine Pylons
Sonaca Group’s experience in fuselage structures extends to interfaces with fuselage-mounted engines. We provide highly advanced parts through topological optimization simulation runs.
Doors
Sonaca has experience in multiple areas of door design and manufacturing: baggage doors, service doors, main landing gear doors. Using composite materials, we are able to manufacture light and robust structures, reducing aircraft fuel burn.
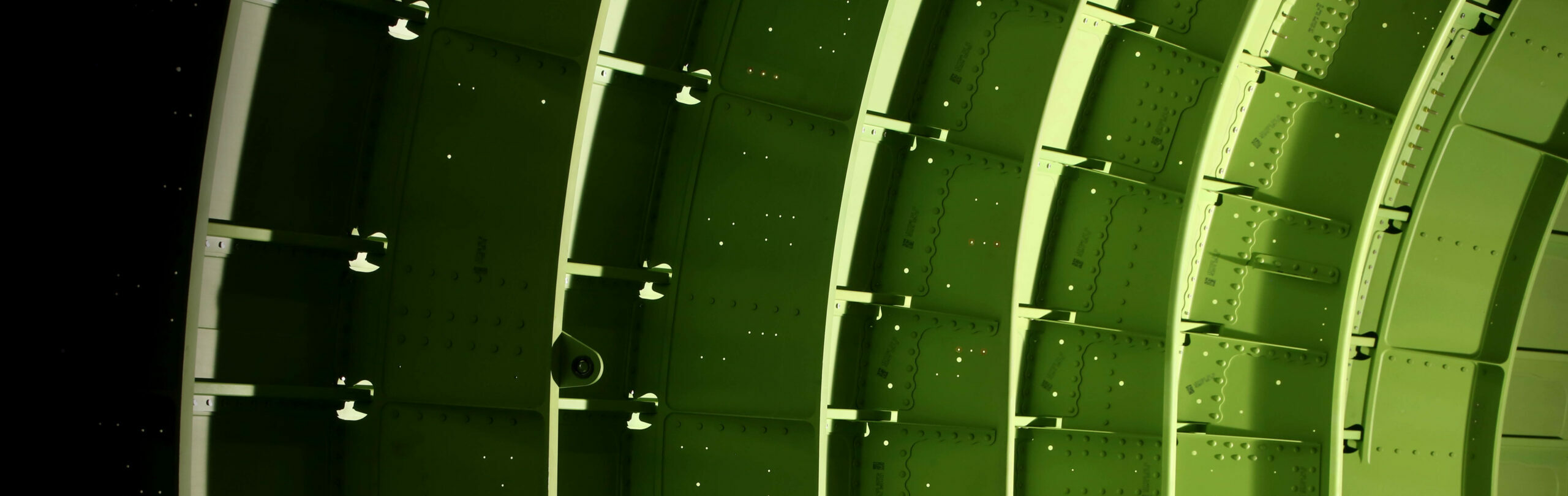
Why we are different
Anti-icing
Electro-thermal and bleed ice protections systems embedded in our slats and fix leading edge are developed and validated within fuel consumption.
Numerical Analysis
For more than 40 years, Sonaca stress office has acquired a huge experience in structural analysis from concept to certification.
Methods
Laying on multidisciplinary teams from conceptual design to serial production, and project management.
Product support
Sonaca also contribute to the support of his products. By addressing an experimented technical team which brings its expertise to the elaboration.
Out of Autoclave automation
As a composite moveable structure manufacturer, Sonaca developed and industrialized Out of autoclave technologies such as SQRTM and RTM.
Certification process
Based on its 40 years experiences as Design and Build partner for major aerospace OEM in certification and qualification.
Green reach
Working at Sonaca, it is caring about its environmental footprint, throughout the whole process from manufacturing to end-use. Sonaca, which 12001 certified.
Design and configuration
From conceptual studies up to detailed definition, Sonaca’s Design department strong expertise in metallic, composite and hybrid structures.
Advanced sealing
Aerodynamic seals installed on aircrafts need to withstand heavy loads in a difficult environment but also deform sufficiently to accommodate 3D large.